Do you know how your building is built? Many building owners see concrete and assume that their asset is conventionally reinforced or precast – the more common types of concrete construction. Post- tensioned (PT) structures are not always properly identified, which can lead to poor maintenance, poor capital planning, and risk of concealed deterioration. Awareness of the structural makeup of your building is vital to maintaining the value of your asset, and minimizing repair costs. It is important for owners of post-tensioned buildings to be aware of the structural implications.
Post-Tensioned concrete structures are reinforced with high strength steel cables, tensioned at high forces, putting the concrete slab under compression prior to supporting any applied loads (furniture, pedestrians, vehicles, snow, etc.). Tensioning cables that have a draped profile lifts the slab between supports, limiting cracking and deflections under load. The main benefits of PT include:
• reduced cracking and deflections;
• longer spans, thinner slabs, fewer columns, and smaller foundations;
• reduced concrete volume;
• reduced carbon footprint during construction from the reduction in raw materials, particularly cement.
PT structures require greater care with respect to water infiltration prevention and management as
water alone can cause PT to corrode. Coring and concrete drilling require additional care because if
a cable is damaged, the failure can be sudden and violent due to the high stresses in the cable.
Cable failures have the potential for the cable to erupt from the structure.
How to Identify PT Structures
There are three primary methods to identify whether a structure is post-tensioned: Design Drawings, Physical Building Review, and Scanning and Exploratory Openings.
1. Design Drawings
If Structural or PT shop drawings are available for review, they may indicate cable bundle locations and forces. Sample Structural and PT shop drawings are shown in Figures 1 and 2 respectively.
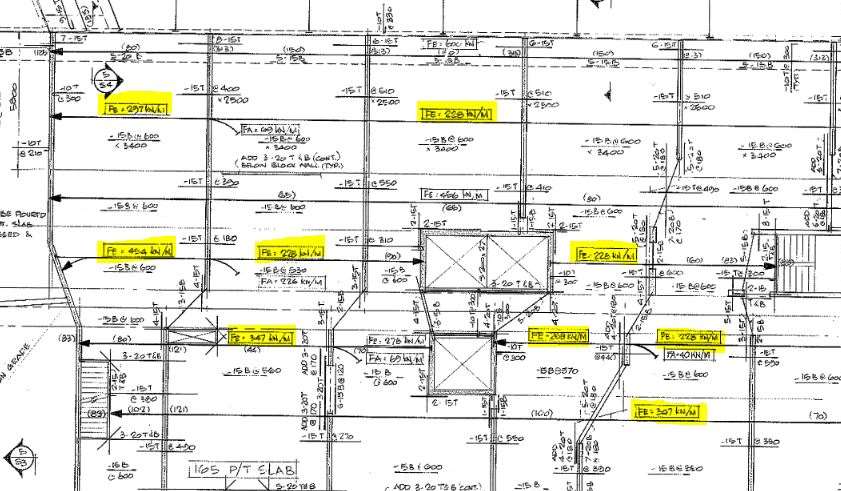
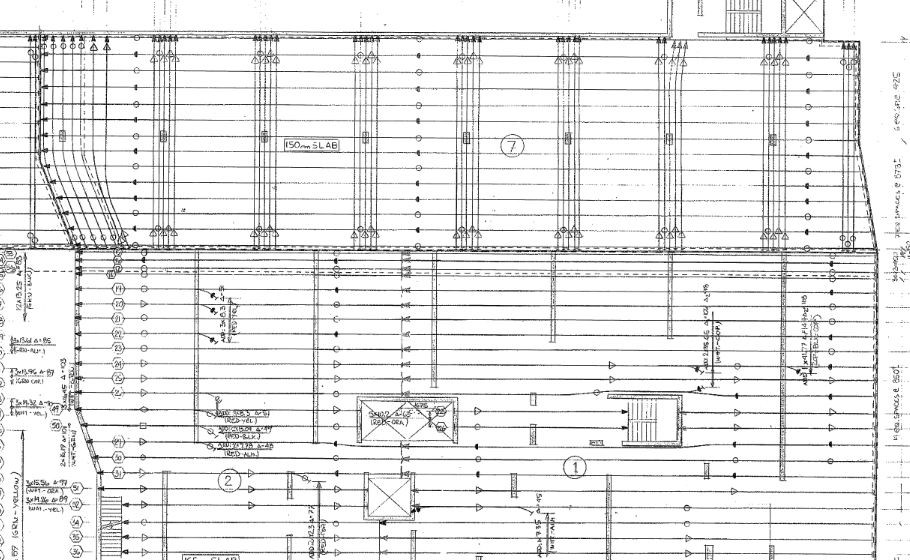
Look for:
- Arrows: Arrows with forces in units of kN/m (kips/ft) and kN (kips). The arrows indicate the intended live (stressing) end while the “T’s” indicate the dead ends.
- The Structural Notes: The Notes may refer to “post-tensioning” or “stressing”.
- The Post-Tensioning Shop Drawings: The complete PT design and layout is illustrated in
the shop drawings, see Figure 3. If available, look at the company in the title block (in Ontario, look for Canadian BBR, Harris PT, DSI, Dywidag, etc.)
2. Physical Signs of PT Components
Post Tensioned structures can also be identified by performing a visual review. If the slab edges are
exposed on the walls, in stairwells, at balconies, etc, there may be visible grout plugs at the live end
anchors. Look for circular stressing pockets filled with a cementitious material, such as in Figure 3. If
the grout plug is dislodged or missing this may indicate cable failure; without a proper grout plug
the anchor is more susceptible to water infiltration and corrosion, see Figure 4.
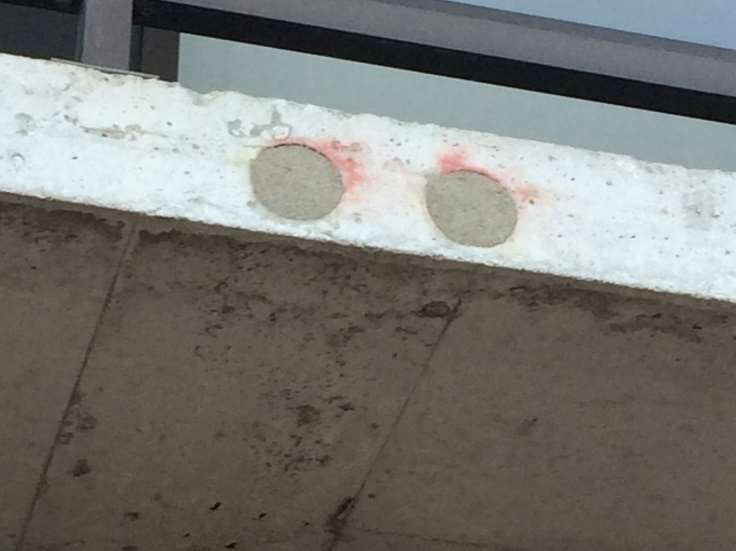
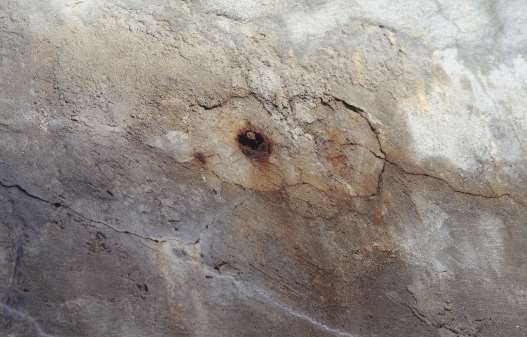
If the PT has been tested in the past, there may be steel cover plates (approx. 400mm x 400mm) at the test locations, see Figure 5. There may also be concrete repairs that protrude from the slab soffit near midspan if PT repairs were previously carried out, see Figure 6.
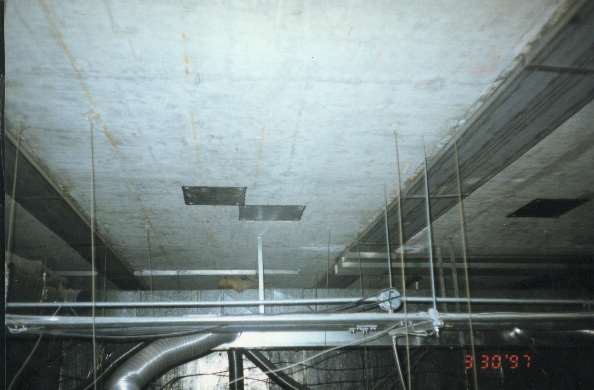
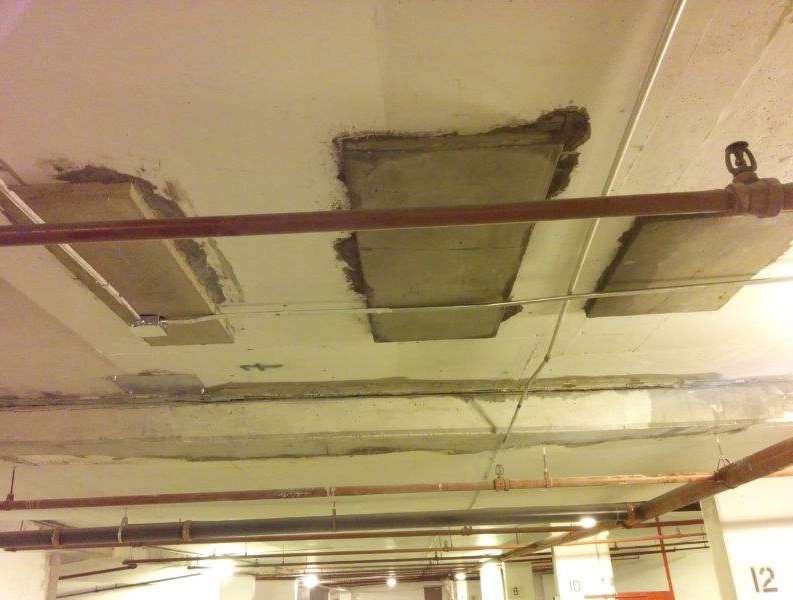
3. Scanning (GPR or X-Ray) and Exploratory Openings
Non-destructive testing, such as Ground Penetrating Radar (GPR) or X-Ray can also be used to check if a slab is post-tensioned. The radiation from X-Rays can be harmful to building occupants and there is therefore a perimeter that must be vacated during testing. GPR is preferable in instances where the surrounding area cannot be vacated for X-Raying. It can sometimes be difficult to differentiate between PT cables and conventional reinforcing steel or other embedded steel. For this reason, exploratory slab openings are often recommended to confirm whether detected steel is post-tensioned.
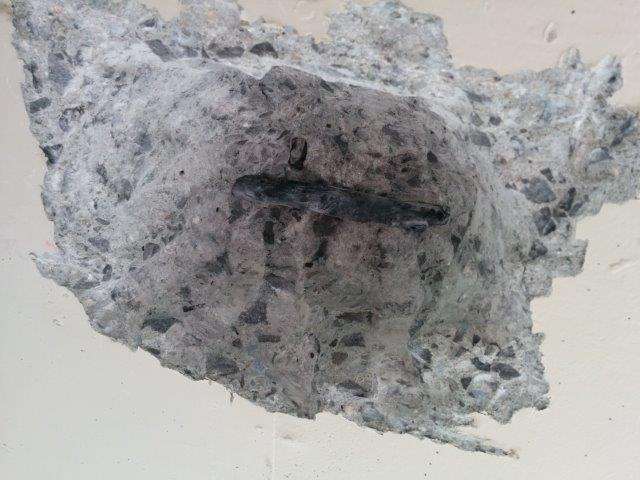
What to do if you have a PT Building
If it is determined that the structure is in fact PT, the next steps are:
- Have a PT Risk Assessment carried out by a qualified professional engineer.
- Monitor and promptly address leakage and condensation along slabs.
- Promptly fix any plumbing/mechanical leaks.
- Ensure that no “blind” drilling or coring is completed.
- Have any concrete repairs carried out by qualified contractors and designed by qualified engineers.
It is important that PT structures be proactively managed to maintain structural integrity, avoid large scale and disruptive repairs, and maintain property value.