This peer-reviewed technical paper was originally published for the Canadian Conference on Building Science & Technology in October 2022.
INTRODUCTION
The volume of wood-framed structures in Ontario has increased since 2015 when the provincial building code was updated to permit wood framed buildings up to six storeys. Wood-framed construction is now common for both townhomes and midrise buildings, many of which offer balconies and terraces for resident enjoyment. A balcony is an outdoor usable space that does not have indoor occupied space below or access to the ground. Wood-framed balconies can be constructed as cantilevered structures (framing joists extend from within the floor framing, beyond the building face to form the balcony, Figure 1) or simply supported (framing joists are connected to a ledger board at the building face, and columns, beams, or other supports are provided at the front edge). A terrace is an outdoor usable space that has indoor occupied space below. Terraces are typically simply supported by walls on all sides and therefore present lower structural risk; however, there is higher risk of damage to the building interior resulting from leaks. In both cases, surfaces are typically sloped to drain water off the front edge or to a drain.
Wood-framed balconies and terraces can be durable and long lasting; however, exposure to precipitation, especially rain combined with snow melt, presents challenges in design, construction, and maintenance. Wood-framed structural building components are susceptible to moisture and must be protected to reduce risk of rot, mould, and structural failure. Since we are focusing on waterproofing systems, we will simply use the term balcony; however, this topic also applies to terraces.
Designers and builders commonly rely on sheet vinyl waterproof membranes to provide waterproofing protection (Figure 2). In these systems, the primary risk areas for water ingress are at penetrations, and terminations. At penetrations, such as a top-mounted balcony guard baseplates, water ingress can cause wood rot compromising guard anchors, creating unsafe conditions and structural concerns. At terminations, such as upturns at the building face or below an access door, water ingress can lead to wood rot, structural issues, and leaks to the building interior.
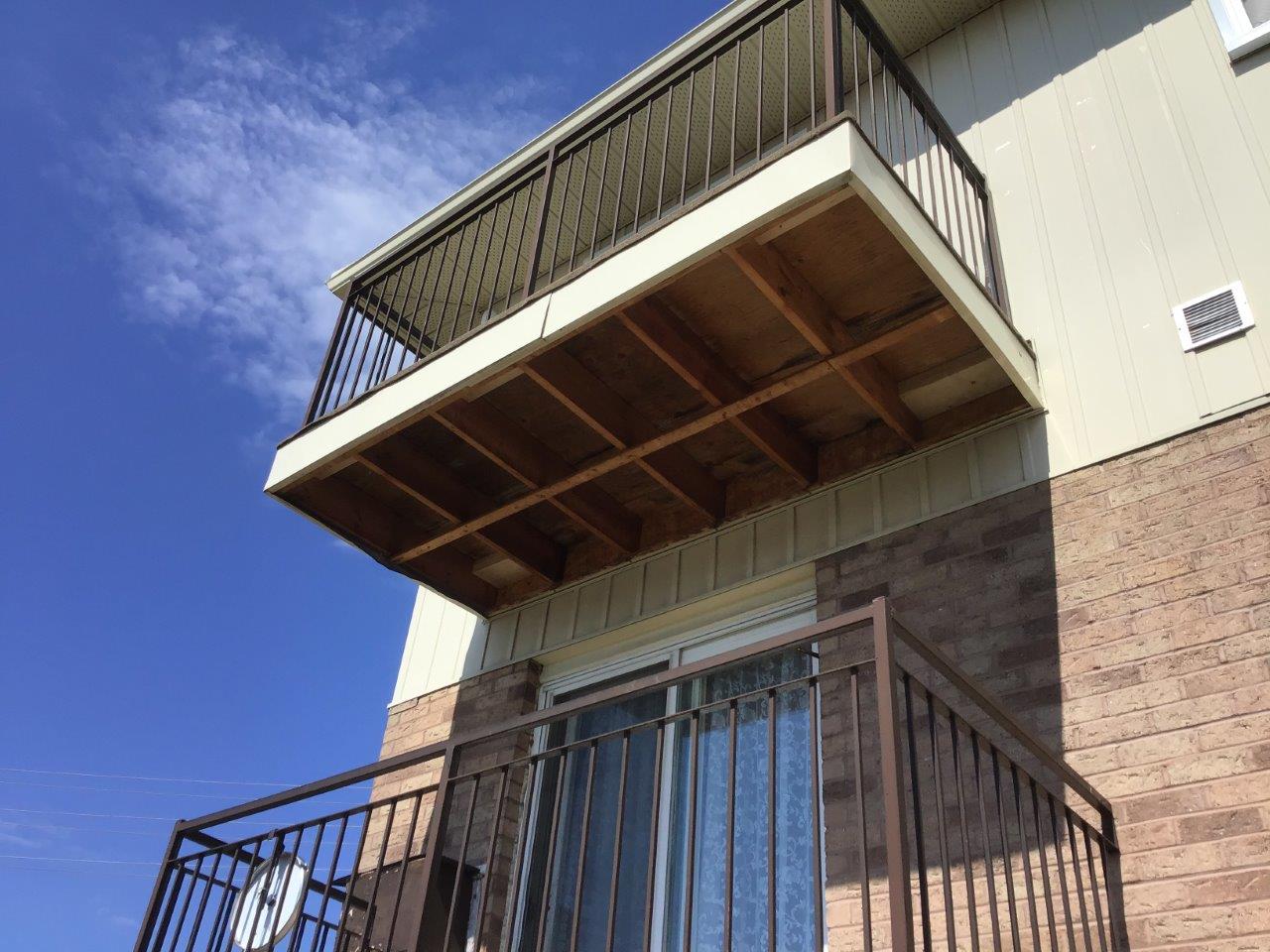
FIGURE 1: Sample cantilevered balcony.
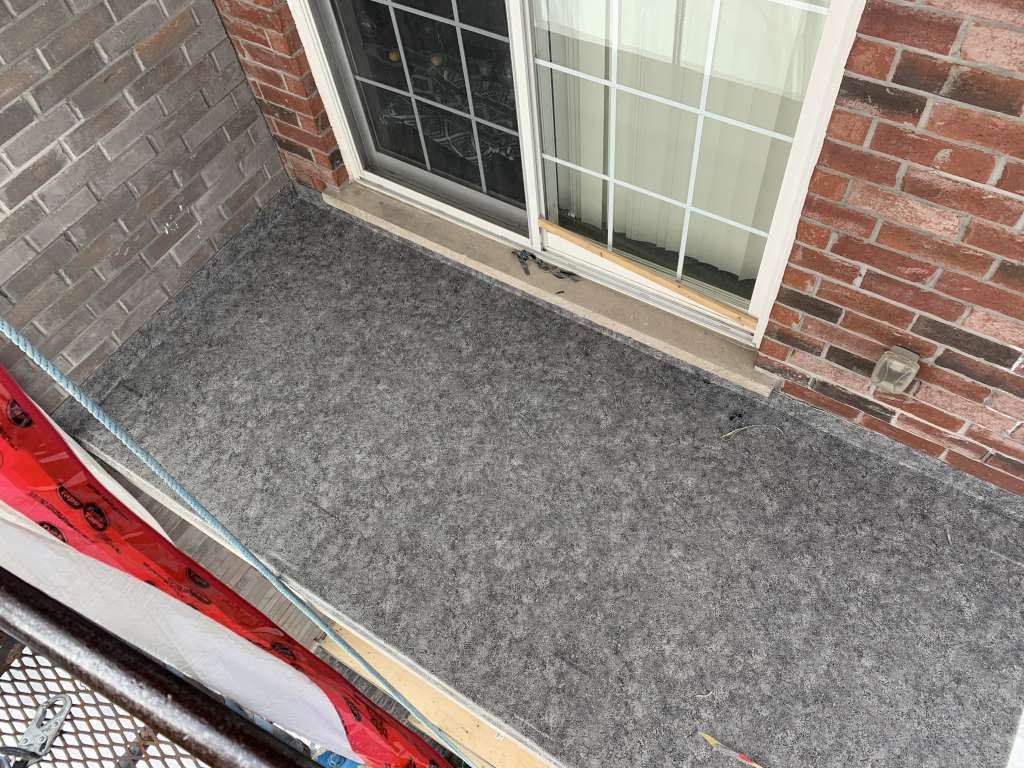
FIGURE 2: Sheet vinyl waterproofing installation.
There are also common issues with water ponding, negative slope, and missing or minimal upturns below balcony door thresholds increasing risk of water ingress. Since wood-framed balcony structural systems are typically concealed from easy visual inspection by architectural details, such as soffit materials on the underside, water leaks can progress significantly before they are detected which presents a risk to public safety.
Identifying and understanding these risk areas is critical to developing and constructing durable wood-framed balconies and terraces. Canadian Standards Association S478:19 Durability in Buildings defines durability as “the ability of a building or building element to perform its functions to the required level of performance for its design service life in its structure environment under the influence of environmental actions.” (Genge et al., 2019). It is reasonably assumed by building owners that the wood framing members provided with protective systems are intended to serve the life of the building, just as they would expect of their walls studs or roof trusses. However, to achieve this service life in wood-framed balconies and terraces require rigor in design, construction, and maintenance of these risk areas.
This paper examines the primary risk areas for water ingress, including balcony guard anchors, the balcony-to-wall transitions, and the access door thresholds for wood-framed balconies and terraces protected by sheet vinyl waterproofing systems. Each area is considered from the perspective of long-term durability, maintenance, and risk, and provides practical alternatives for details commonly applied in Ontario.
PENETRATIONS
Sheet vinyl waterproofing penetrations present high risk for water ingress leading to wood rot. Where possible, penetrations should be avoided altogether or elevated off horizontal surfaces where water is expected to collect. Where penetrations are required, durable seals must be provided since the waterproofing membrane is not self-sealing. The most common and highest risk penetration at horizontal surfaces with high exposure is at balcony guard baseplate anchors.
Guards, also referred to as railings, are an integral safety component of any balcony or terrace. The Building Code specifies loading and dimensional requirements for guards. In Ontario, guards are commonly top mounted on both concrete and wood balconies. The guard is structurally connected to the balcony with vertical anchors. In wood balconies, the anchor holes penetrate the vinyl waterproofing membrane and anchors often rely on direct pull-out resistance where water penetration can quickly reduce anchor strength. Anchor penetrations must be provided with a durable watertight seal to maintain guard safety (Figures 3, 4).
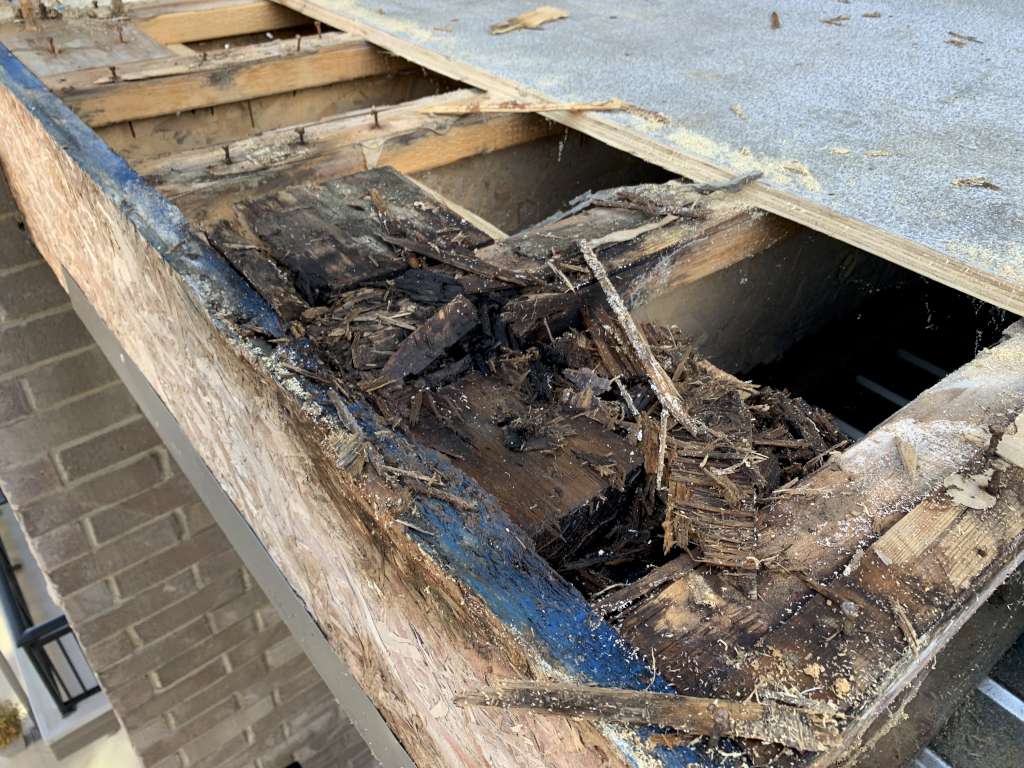
FIGURE 3: Deterioration below guard baseplates after ~7 years.
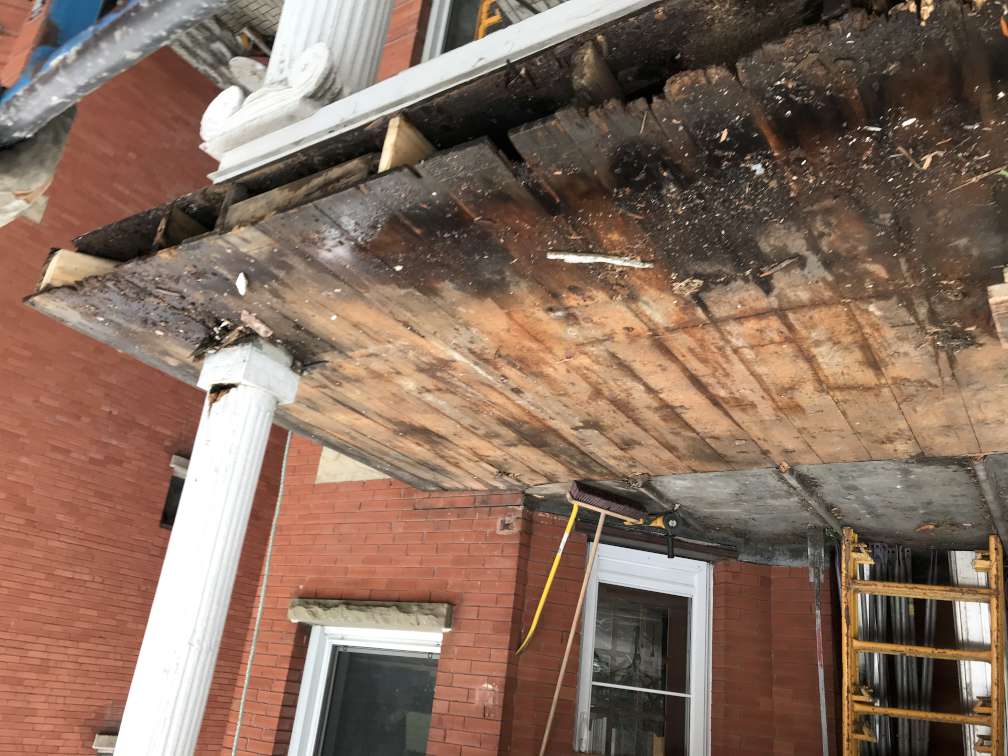
FIGURE 4: Deterioration below guard baseplates at dimensioned lumber.
Additionally, top-mounted guard baseplate securement methods often create depressions around the baseplate that attract water thereby increasing the severity and duration of exposure to moisture. Defects under these conditions cause accelerated deterioration. During installation, guard baseplate anchors are fastened through the baseplate, waterproofing and wood sheathing, and into the structural wood blocking. Achieving the required torque for structural securement commonly compresses the waterproofing and wood sheathing which creates a depression and allows water to collect around the baseplate (Figures 5, 6).
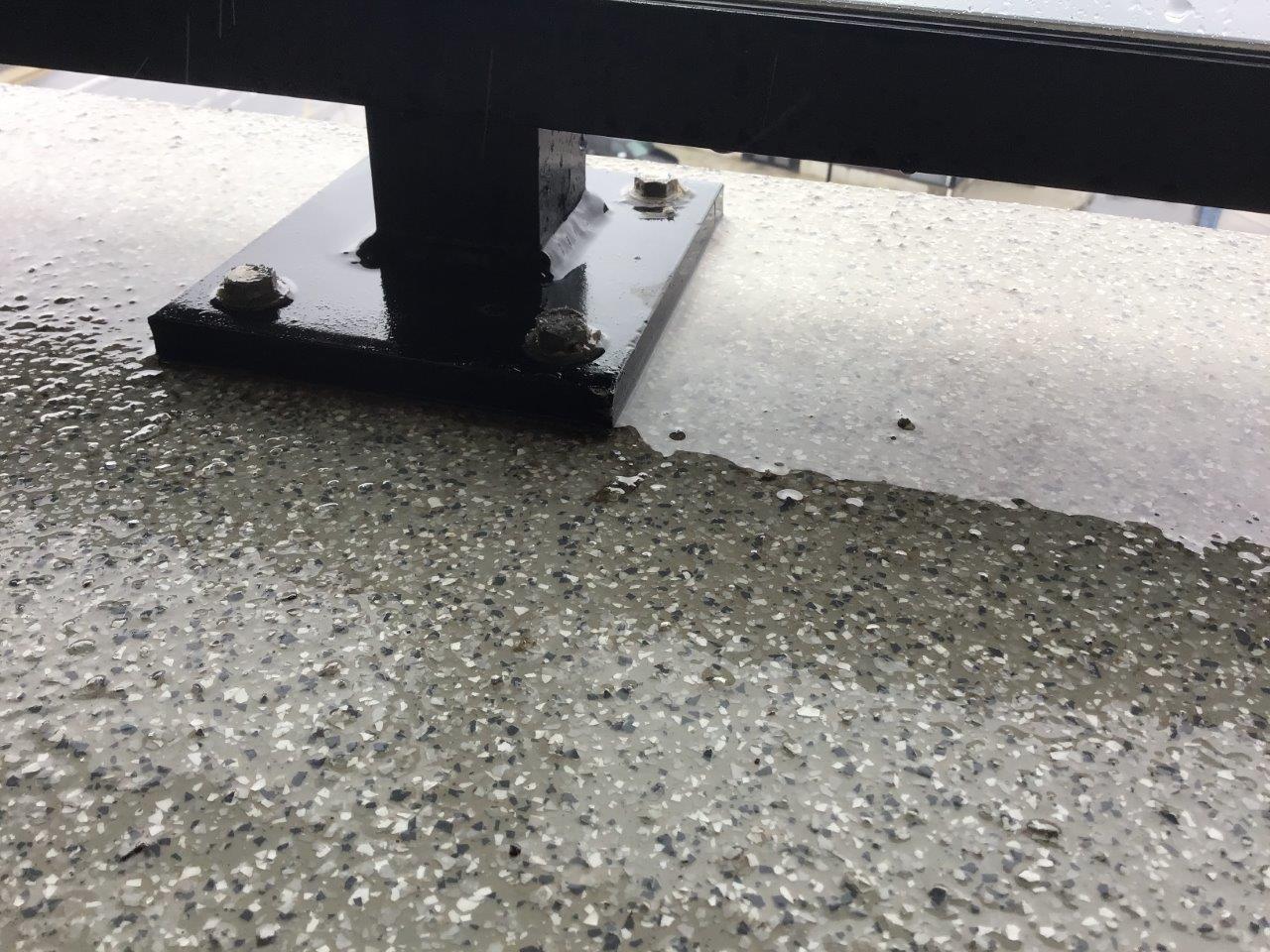
FIGURE 5: Typical depressed baseplate with ponding water at new construction.
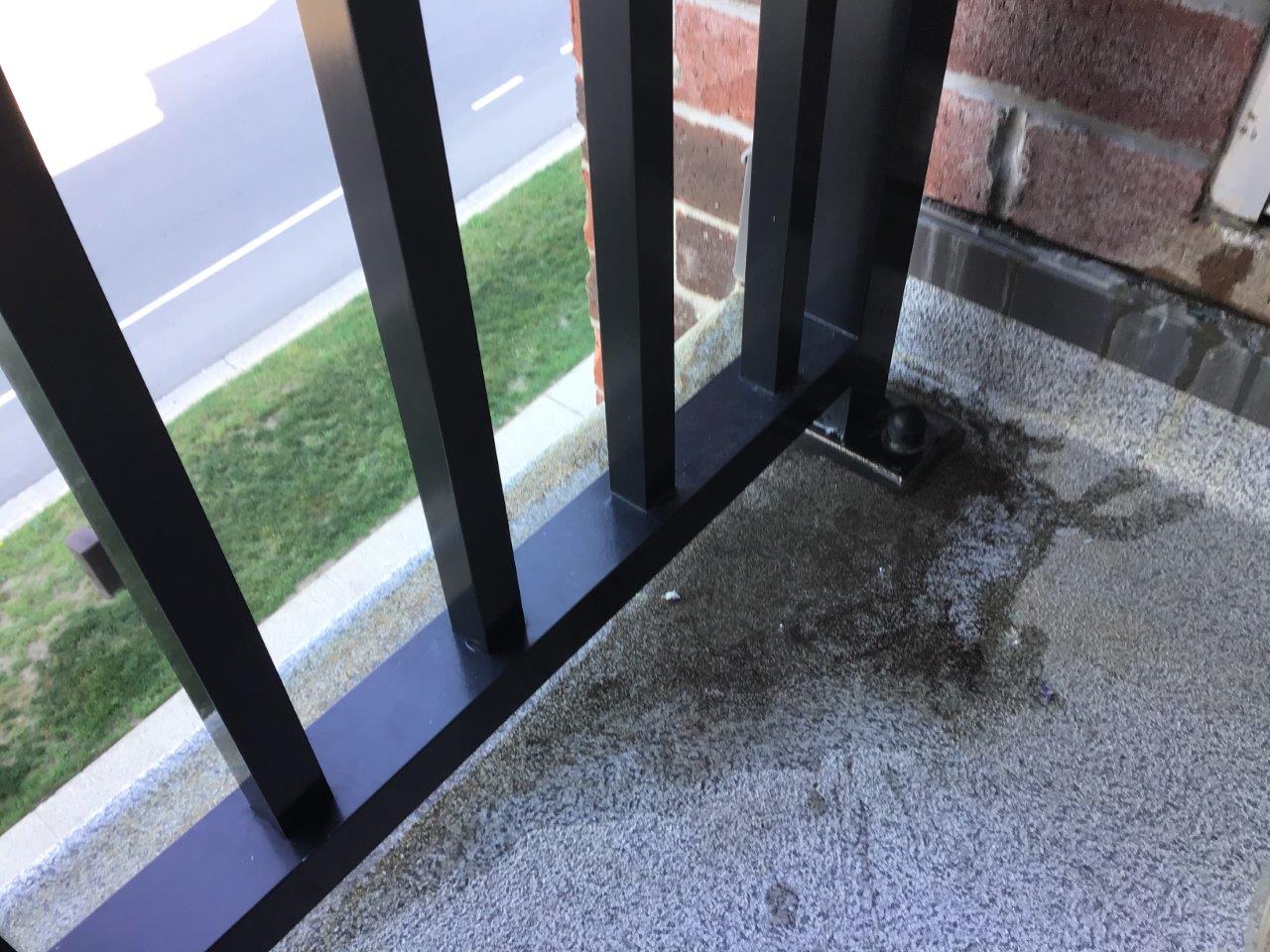
FIGURE 6: Typical depressed baseplate with ponding water at existing building.
This risk is commonly addressed through perimeter sealant around the baseplate, sealant within the anchor holes, or a butyl gasket below the baseplate. These approaches can be combined for added redundancy.
BASEPLATE PERIMETER SEALANT
Installing sealant around the perimeter of the top-mounted baseplate is a simple but ineffective solution to protect the penetrations. Relying on sealant is risky due to increased variables including proper material selection, compatibility, surface preparation, workmanship, and maintenance. De-bonded or damaged perimeter sealant is common and inevitable since the service life of the sealant is 10-15 years at best, compared to 20-30+ for the waterproofing and guards. This presents major durability concerns, since even a small imperfection in the seal presents a source for water entry (Figure 7).
In some cases, the perimeter sealant is provided with a gap, or weep hole, at the front edge to allow any water entering the guard post to drain out. Drain holes are provided at guard post bases to drain water entering the guard assembly through joints which is a direct bypass of the perimeter sealant and contributes to water entering the anchor penetrations. There are clear risks with providing a gap in the baseplate perimeter sealant, especially when considering that the baseplates may be set in depressions created when the guard is anchored. Even though the weep hole is on the positively sloped side of the balcony, it now sits lower and is an easy source for water entry.
Further, the detailing at the balcony drip edge flashing may prevent drainage, and instead direct water back toward the weep hole (Figure 8). This is reviewed in more detail later in this paper.
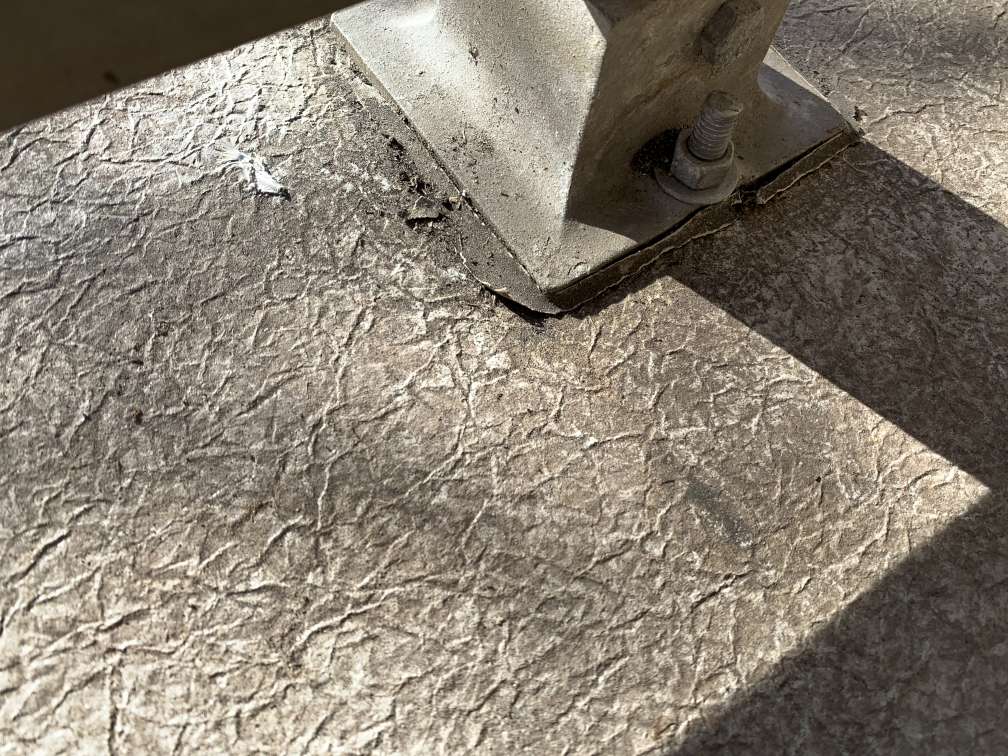
FIGURE 7: Debonded perimeter sealant at top-mounted guard baseplate.
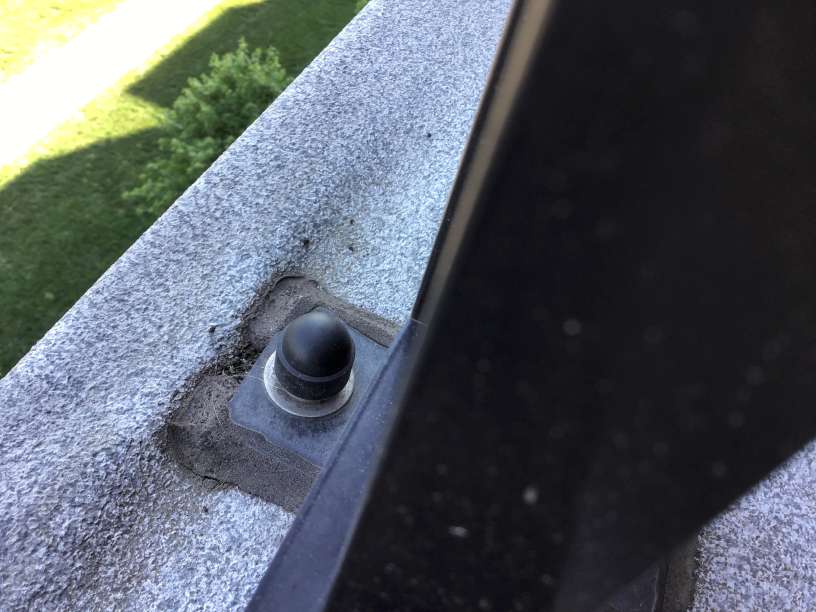
FIGURE 8: Perimeter sealant weep hole and back-slope at front edge of balcony.
BUTYL GASKET BELOW THE BASEPLATE
A butyl gasket or pad may also be placed below the guard baseplate to provide a seal to protect the anchor penetrations (Figure 9). However, when the pads are either not fully engaged (Figure 10) or skewed the anchors are vulnerable to water entry. Additionally, if adhesive pads are used but the release film is not removed, the seal will be compromised.
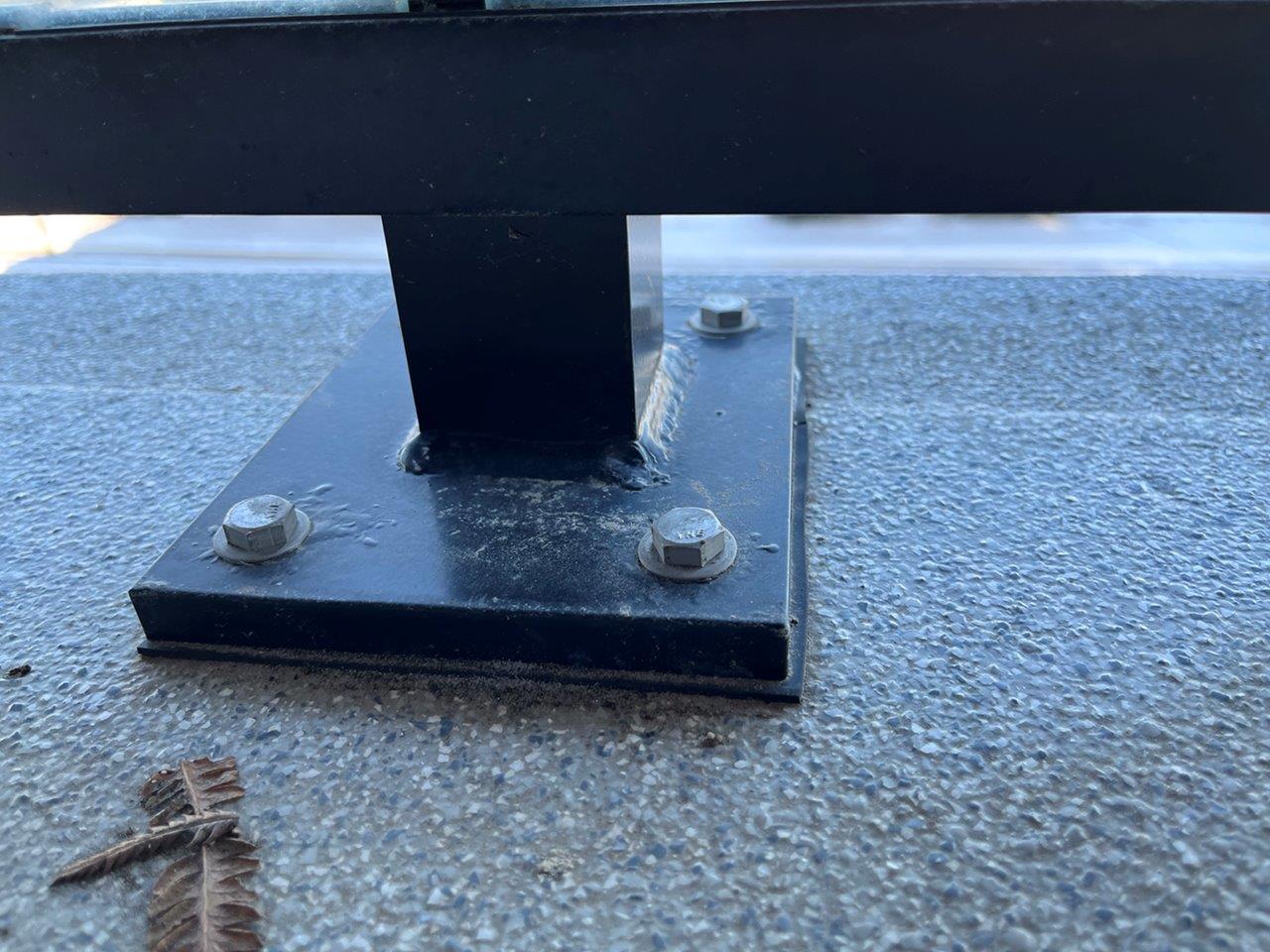
FIGURE 9: Gasket provided below guard baseplate.
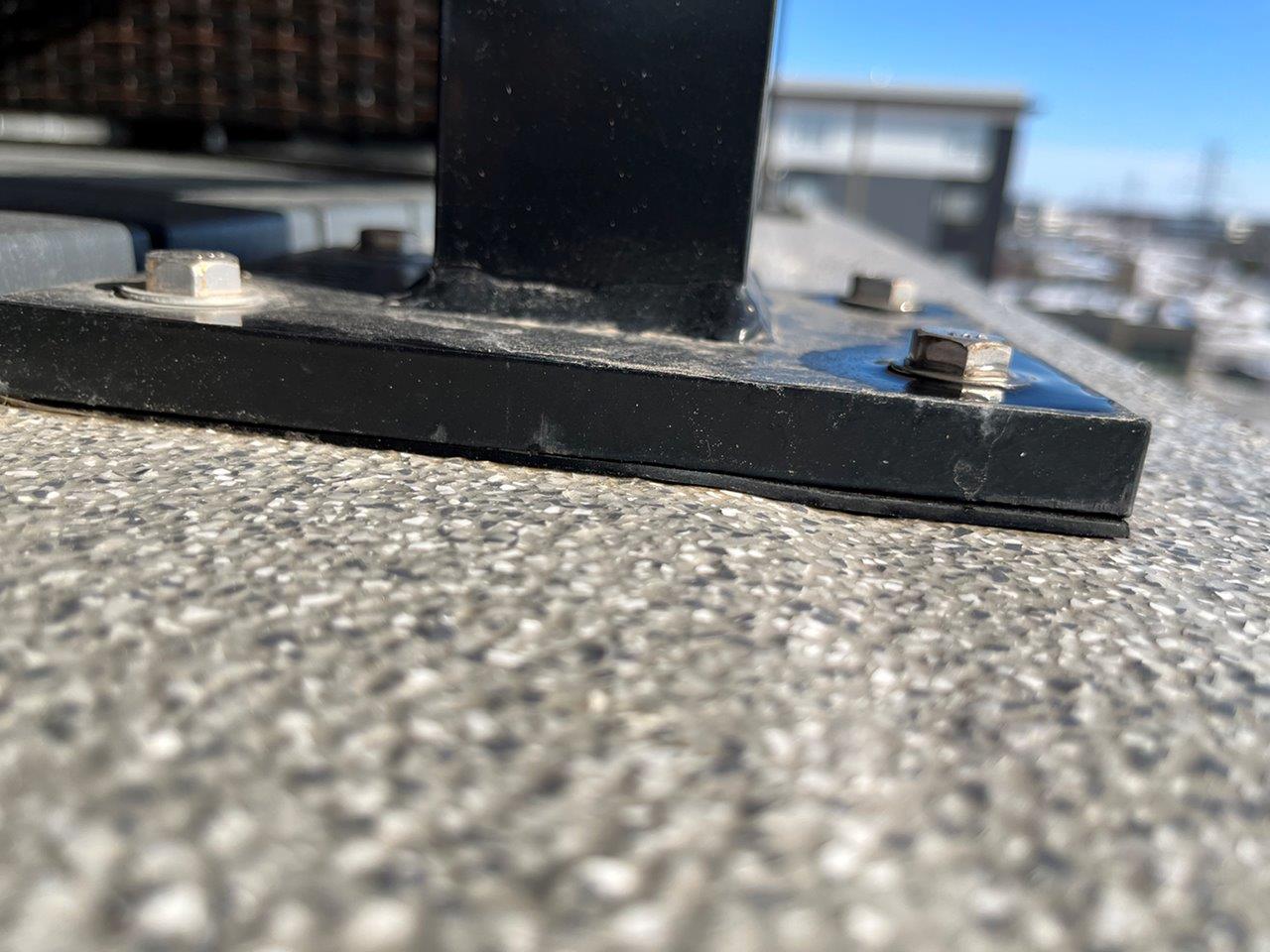
FIGURE 10: Gasket not engaged below guard baseplate.
ANCHOR PENETRATIONS
To provide a seal directly at anchor points, the anchor pilot holes are filled with sealant prior to installing the fasteners (Figure 11). In general, this approach is effective. However, there is still a risk of water entry as the sealant ages and fails or poor levels of protection if not installed correctly. Since it is concealed, the integrity of the seal cannot be confirmed on installation and regular inspection or maintenance of the sealant itself is not feasible. During investigative reviews of new construction, there may be areas with no protection at the penetrations at all (Figure 12).
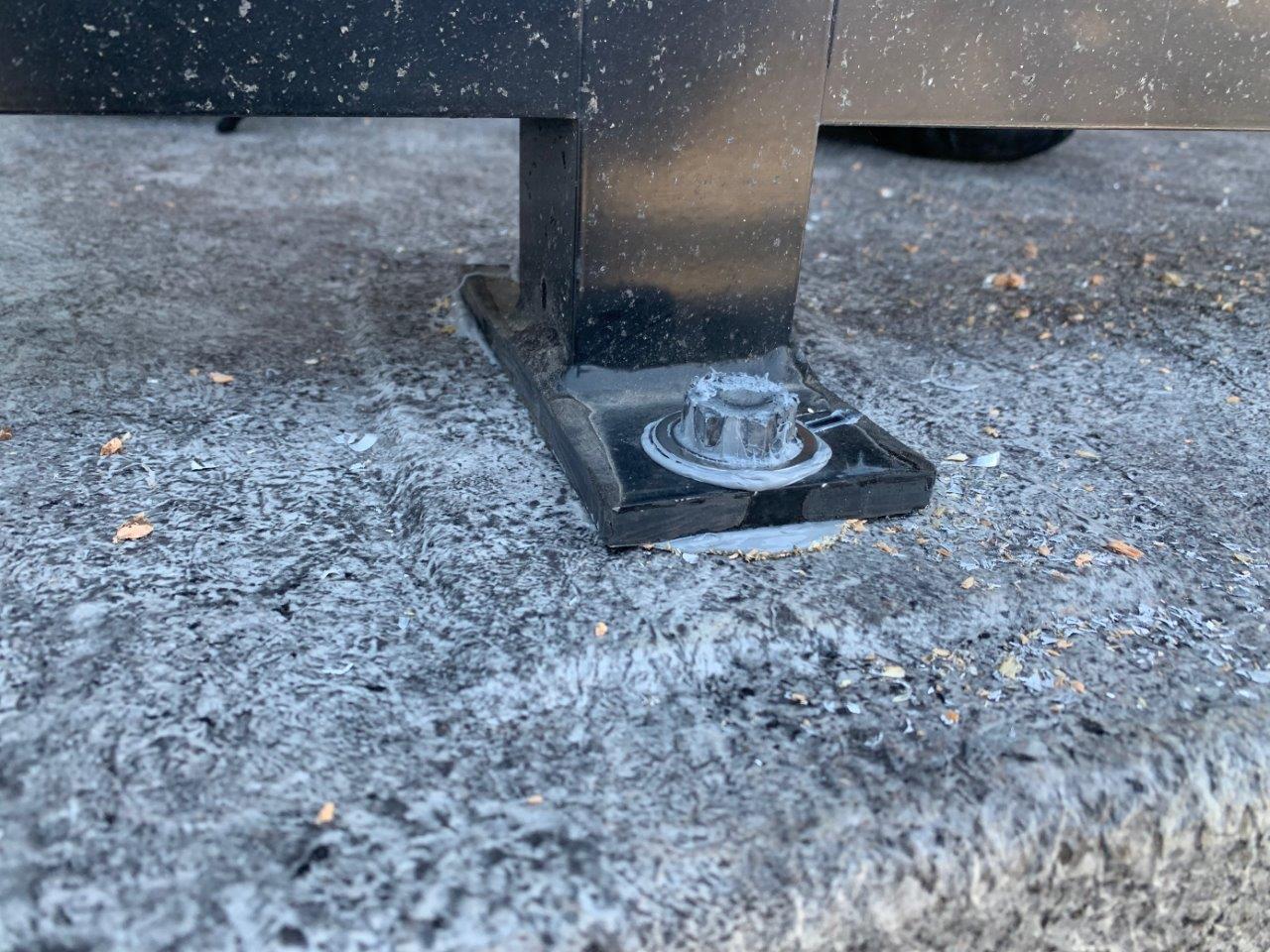
FIGURE 11: Sealant filling the guard anchor pilot hole after fastener installation.
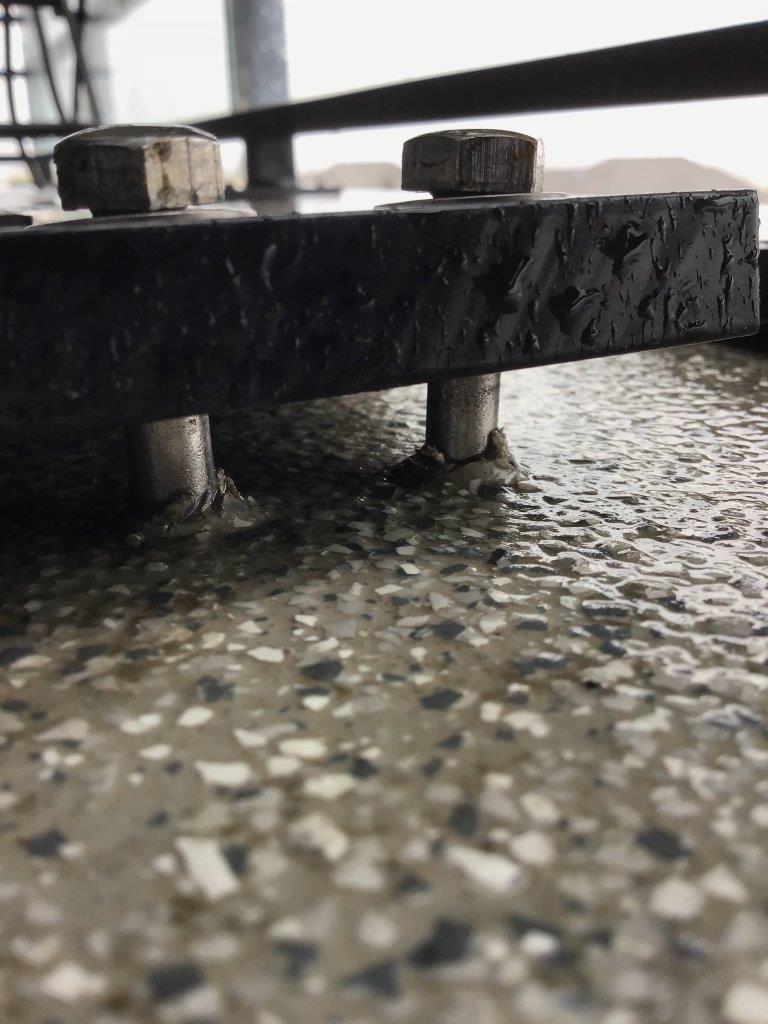
FIGURE 12: Unsealed fasteners penetrating directly through membrane at new construction.
LAG BOLT VS. THROUGH BOLT ANCHORS
Lag bolts are commonly used to secure guard baseplates because they are easy to install and do not require access to the balcony underside. This is common in new construction, where balcony waterproofing and soffits have been installed by the time the guard installation crews arrive on site. Using through-bolt anchors in lieu of lag bolts provides additional redundancy in maintaining guard securement. A threaded rod (or carriage bolt) is installed from the baseplate to the underside of the structural wood blocking, terminating with a washer or plate and nut. This changes the structural connection from relying on pull-out resistance of the lag bolt to the bearing capacity of the washer or plate and nut on the underside of the wood blocking. Since the risk is that water is going to enter from the top side of the balcony and deterioration will inevitably occur, lag bolts are much more susceptible to loss of structural capacity due to wood rot and deterioration within the anchor penetration. Using through-bolts reduces the risk of total failure of the guard as the bearing capacity is dependent on the surface farthest away from the water entry point. Where guard baseplates align with framing joists, lag bolts can be used in combination with through-bolts.
RAISED BASEPLATES
Where top-mounted guards are used, managing the risk of water entry on the horizontal surface is critical. Raising the baseplates higher than the field of the balcony (Figure 13) allows for water to be deflected around the anchor penetrations, providing inherent protection. This approach does not eliminate the penetrations in the horizontal surface but is a strategy for risk mitigation and redirection of the water. A curb, wood blocking, or aluminum shims can be used to raise the baseplate. Consider guard dimensions, including height, climb-ability, and opening size relative to Building Code Requirements. If re-using existing guards, alterations may be required. Many newer guard systems can accommodate raising baseplates without exceeding maximum allowable opening size from the top surface of the balcony to the underside of the bottom rail (Figure 14). Re-using existing guards can provide substantial cost savings.
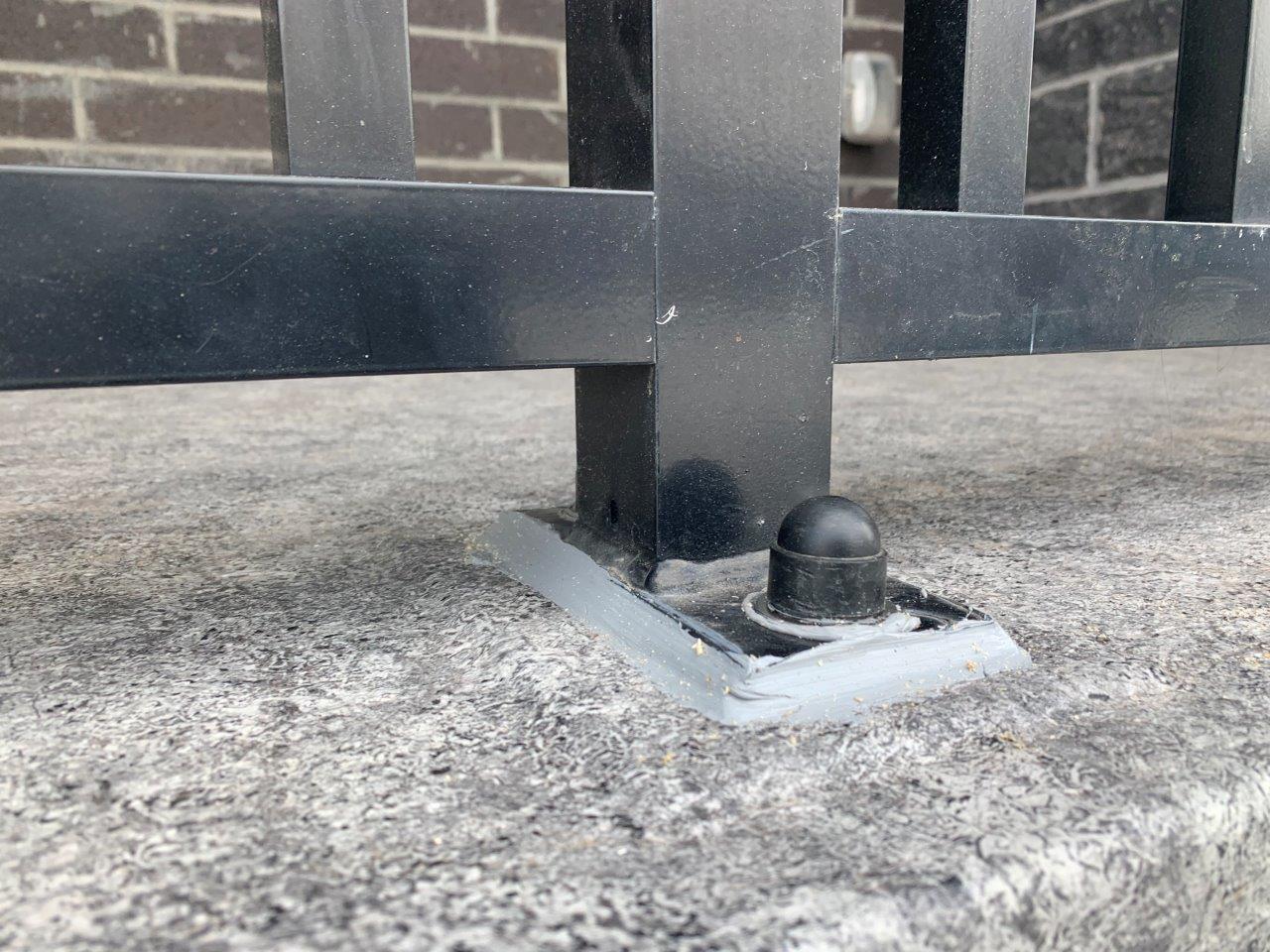
FIGURE 13: Baseplate raised with a plate below to prevent pooling water around horizontal penetration.
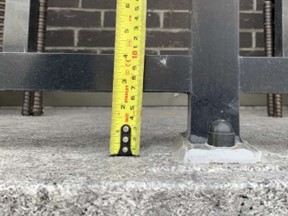
FIGURE 14: Guard max opening size maintained below 100mm despite raising baseplates.
SIDE-MOUNTED AND WALL-MOUNTED GUARDS
In lieu of top-mounted guards, side-mounted guards are a reasonable alternate to minimize the impact of penetrations through the membrane. Continuity of the membrane and providing a gap between the rim joist or fascia and the guard rail for drainage and drying are key considerations for this design to work. Transitioning away from top-mounted guards may be critical to address these issues in the long-term. If implementing on existing balconies in a restoration setting, there may be increased costs for new structural design and blocking installation required to accommodate the side-mounted guard.
Side-mounted guards also eliminate the risk of fasteners connected only to sheathing. Although a common structural and procedural issue with top-mounted guards, it is beyond the scope of this paper.
Another approach is to have wall-mounted guards and avoid penetrations through the membrane at anchor points altogether. Guards may be connected to adjacent wall assemblies, columns, or structural posts. There are other risks associated with this approach that must be considered; however, these are beyond the scope of this paper.
TERMINATIONS
Sheet vinyl waterproofing terminations also present high risk for water ingress leading to wood rot. Terminations include perimeter upturns at balcony doors, cladding and columns, and downturns at balcony slab edges.
UPTURNS
Upturns at balcony doors, cladding, and columns require membrane flashing upturns to prevent rainwater and snow build-up/melt from getting behind the membrane. A sealed upturn with a minimum height of 100mm (4”) to 150mm (6”) is appropriate for most installations where the waterproof membrane does not interface with an adjacent through-wall or sub-sill flashing. A durable detail requires a minimum upturn height, securement, and a durable seal at the top edge of the membrane. The seal at the top edge should also be protected with a metal flashing and sealant, providing further redundancy.
Where upturns are not sealed – or where the termination is sealed, but there is no upturn at all – the wood structure is at extremely high risk of exposure to water. Inside and outside corners at upturns present additional detailing challenges and risks.
At upturns, sheet vinyl waterproofing is adhered to the adjacent building material (such as brick or wood sheathing) and the top edge is sealed with sealant to prevent water penetration. As the adhesive ages and fails and where there is no additional restraint the waterproofing will debond and come loose (Figures 15, 16), increasing risk of water penetration and further debonding of the vinyl waterproofing sheet.
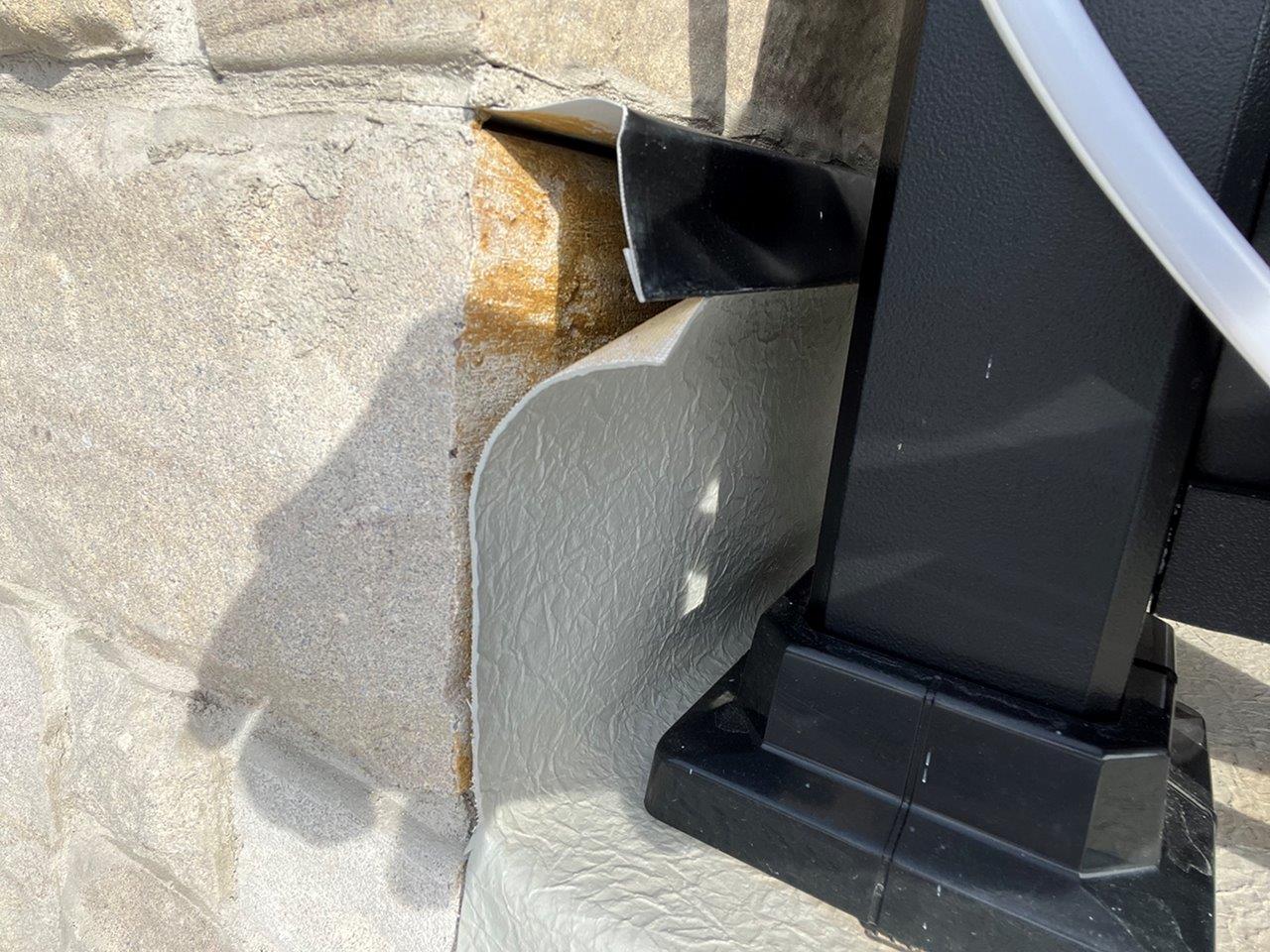
FIGURE 15: Debonded upturn at cladding.
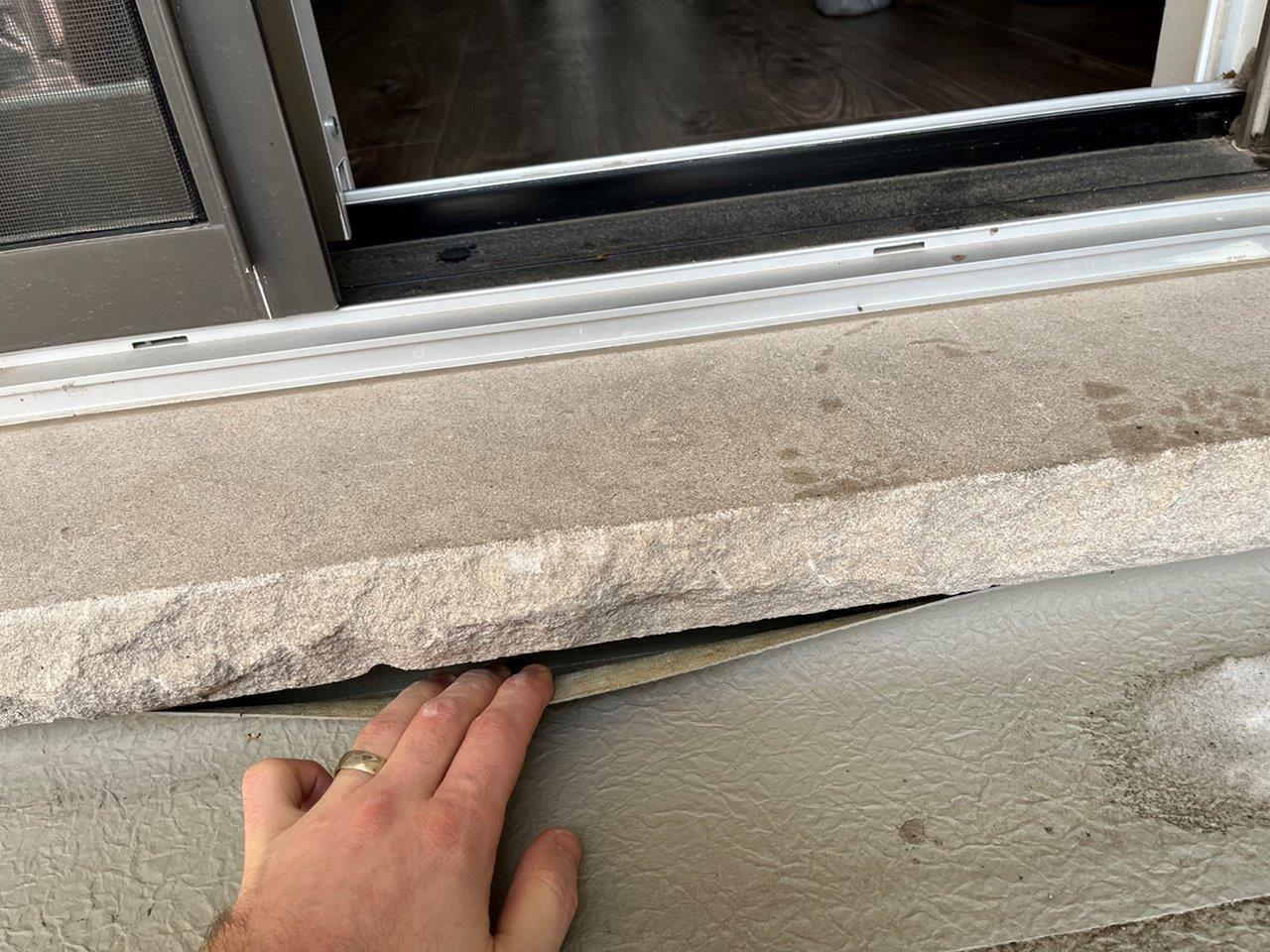
FIGURE 16: Debonded upturn at balcony door sill.
Rather than relying solely on the adhesive for membrane securement, a fastening bar should be used to provide mechanical restraint. A weather tight seal can be provided at the membrane layer by providing self-sealing butyl tape against the membrane prior to fastening bar and fastener installation. Further redundancy against water penetration can be provided by a prefinished metal counterflashing terminated into a sealed reglet to protect the top edge of the membrane and conceal the fastening bar.
The same watertightness and redundancy principles apply at inside corners, outside corners, and post penetrations. Cuts and seams should be reduced or avoided where possible by folding the membrane, at inside corners for example. Protect all upturns with continuous fastening bars, seals, and counter flashings.
NO UPTURN
When sheet vinyl waterproofing is not upturned onto an adjacent building material, the waterproofing is typically terminated with a bead of sealant. There is no water management redundancy with this approach. As the perimeter sealant ages and fails (Figure 17), water penetration around the vinyl waterproofing sheet is inevitable. At balcony doors, this can result in ledger board deterioration or detachment, or wood rot at a critical location of a cantilevered support beam. Further, this presents high risk of water leaks into the wall system and building interior.
At columns, this can result in wood rot (Figure 18) and rapid loss of structural capacity. Further, this issue is often concealed from view or easy inspection by metal flashings and balcony enclosures and soffits. Like balcony guard baseplate penetrations, this mechanism does not result in a water leak to the building interior. Water penetration can continue unchecked for years as deterioration progresses. Locations with no upturn are not durable and should be avoided.
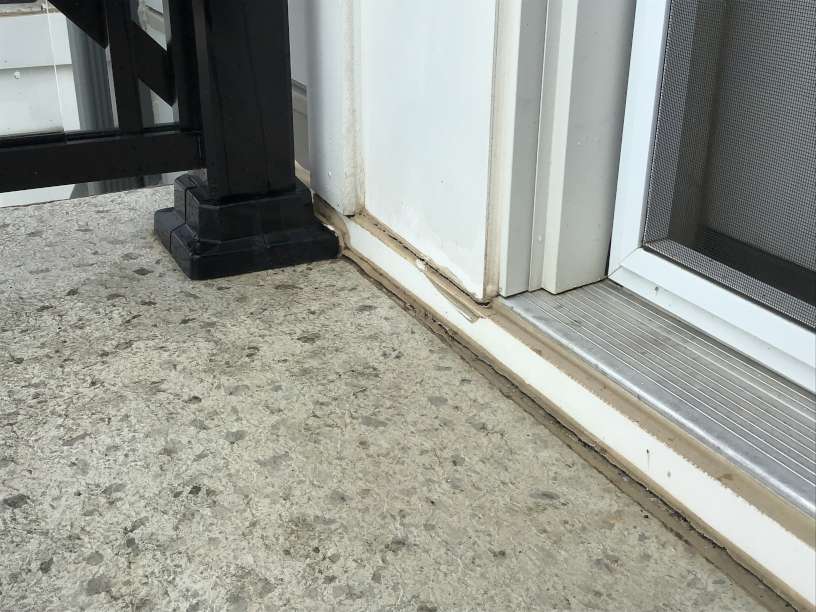
FIGURE 17: No upturn at balcony door or cladding.
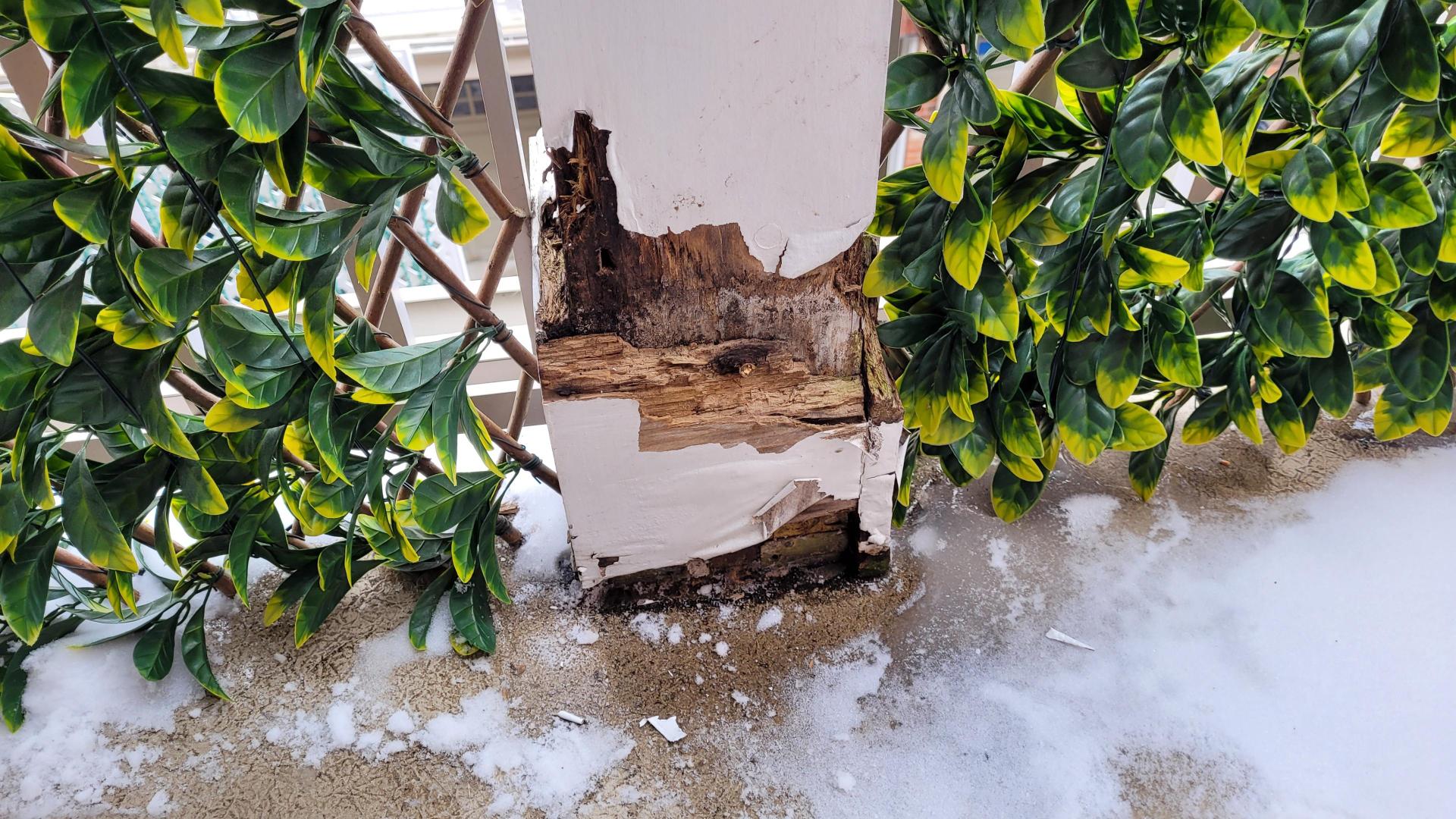
FIGURE 18: No upturn at structural column resulting in wood rot.
DOWNTURNS
At the front edge of a balcony, sheet vinyl waterproofing is terminated on a prefinished metal drip flashing. Metal drip flashings are typically fastened down onto the horizontal surface of the balcony with the drip extending beyond the balcony surface. The membrane is then adhered to the wood sheathing substrate and metal drip flashing, and the front edge of the membrane is terminated at the drip edge in a sealed plastic clamp. In this configuration, the thickness of the metal flashing on the horizontal surface creates a lip at the balcony edge. If there is insufficient balcony slope, this lip can cause water to pond near the balcony edge – and around top-mounted guard baseplates if applicable. Further, as the membrane ages and shrinks the waterproofing at the front edge of the balcony pulls on the metal drip flashing, causing the front edge to rise. This exacerbates the ponding water issue and increases risk of water penetration at top-mounted balcony guard baseplates.
The key culprit in this approach is the metal drip flashing. If the drip flashing is instead installed vertically on the balcony rim board and fastened horizontally, the waterproof membrane will maintain slope as it ages. This eliminates risk of ponding water at the front edge and balcony guard baseplates. A durable repair is completed with a sealed metal clamp at the drip edge (Figure 19), combined with water diverters and sealant end dams (Figure 20) at the balcony-to-cladding interfaces to direct water onto the drip edge. A fastening bar can also be installed on top of the waterproof membrane along the front edge.
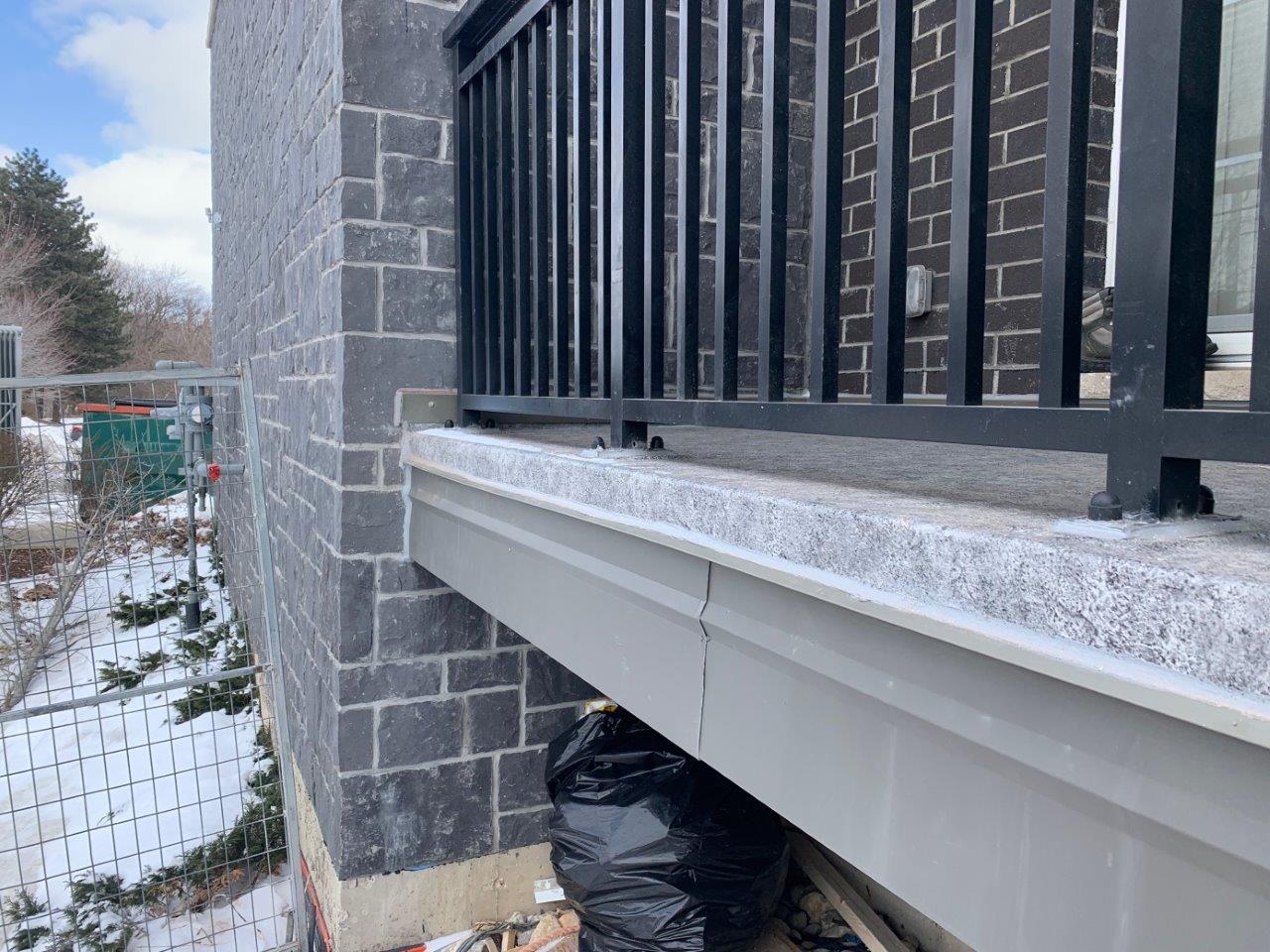
FIGURE 19: Metal clamp at leading edge of waterproofing. Concealed – drip flashing fastened to rim board, not field of balcony.
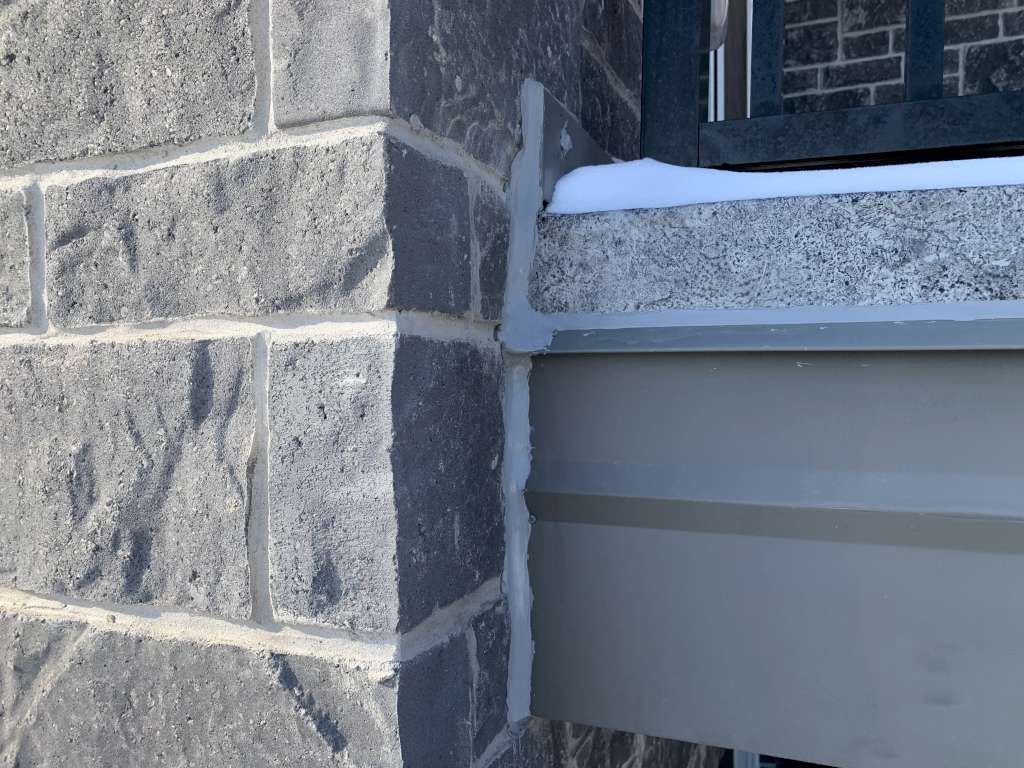
FIGURE 20: Sealant end dams to direct water onto the drip edge.
INTERFACES
Where possible, balcony waterproofing terminations should tie-in to the water control layer of adjacent building systems to provide continuous drainage. At balcony doors, the door should have a raised threshold and sub-sill flashing ship-lapped on top of the balcony waterproofing upturn, secured with a fastening bar. At rainscreen cladding interfaces such as masonry or siding, a through-wall flashing should be provided above the surface of the balcony to allow for a proper upturn and ship-lapped interface. It is important that the building systems remain decoupled to address system repairs separately. For example, allowing the balcony waterproofing to be replaced without the need to remove the balcony door.
DRAINAGE
Balconies with solid balustrades are typically provided with a scupper drain or floor drain. The balcony should be properly sloped by shimming on top of the wood joists, and the area around the drain should be set lower to encourage drainage. A major risk with balconies with balustrades in the Ontario climate occurs when there is snow and ice buildup followed by a rain event. The snow and ice will block drainage, resulting in water building up on the balcony. This can cause the water to overflow the membrane upturns or door thresholds resulting in major water penetration issues. It is critical that overflow scuppers are installed above the level of the deck yet below the lowest upturn elevation.
MAINTENANCE, MONITORING, & REPAIRS
Regardless of the quality of detailing, completing diligent maintenance and monitoring are critical to maintain a watertight membrane. Snow and ice removal, sharp objects, or heavy furniture can also cause membrane tears or damaged seams. Maintenance should include periodic inspection for punctures and cleaning to confirm water is draining effectively off the balcony surface. This is particularly important where deck boards are provided on the balcony, concealing the waterproofing surface. It is also critical to conduct frequent inspections for concealed components to confirm structural safety and to identify issues before they become widespread or a structural issue. Vinyl or aluminum soffit materials should be perforated to allow wood elements to dry. Where solid soffit materials are provided and it is not cost-effective to remove, access panels should be installed.
Monitoring is particularly important at engineered joists, since some manufacturers will not provide a splice repair detail, instead stating the full joist (all the way into the building) should be replaced. Where localized repairs are required to address damaged wood framing and sheathing, full waterproofing replacement should be considered to avoid back-lapped or unreliable seals at membrane seams. Identifying deterioration early – or preventing it altogether – is the first objective.
KEY CONSIDERATIONS
The following are key considerations when working with wood balconies or terraces protected by sheet vinyl waterproofing membranes:
- Pay Attention to Details: Wherever possible, provide redundancy in detail design at penetrations and terminations and conduct reviews during construction to confirm compliance. Pay particular attention at top-mounted guard anchor penetrations. Use side-mount or wall-mount guards where possible to avoid waterproofing penetrations. Always provide upturns and consider interfaces.
- Provide for Drainage and Drying: Provide balconies with positive slope to drain, especially at top-mounted balcony guard baseplates. Provide flashings, drip edges, and deflectors to direct water away from the balcony surface and building face. Consider other moisture sources such as planters, eavestroughs, or cladding interfaces. Provide ventilation for wood elements to dry by providing perforated soffit materials. Provide for overflow scuppers at terraces with balustrades.
- Inspect Frequently: Conduct frequent inspections of concealed structural components and of readily visible waterproofing details to confirm safety. Check for damage to the membrane. Provide access panels at soffits to accommodate these reviews.
REFERENCES AND ADDITIONAL RESOURCES
- Genge et al., Canadian Standards Association, April 2019, Durability in Buildings (CSA S478:19), page 12.
- BC Housing, Illustrated Guide for Building Safe and Durable Wood Decks and Balconies, https://www.bchousing.org/publications/IG-Building-Safe-Durable-Decks-Balconies.pdf, accessed April 30, 2022.