Considering Window Replacements in the Next Few Years?
Poor performing older windows are often drafty, they allow significant heat gain in the summer, and are cold in the winter. Replacing windows is a big undertaking and it’s easy to get overwhelmed by the costs and construction coordination alone. We often find that many standard window design details are chosen and opportunities to optimize these details to save money and increase performance are overlooked.
Before we jump into things, here are some quick window facts:
- Windows include the glass and frames
- Installing new windows presents a rare opportunity to improve your building since they directly impact utility costs, resident comfort, views, property values, and aesthetics
- There are over 4000 different types of coated glass
- There are nearly infinite configurations of frames that can be optimized to improve views and change building appearance
- Arguably the most viewed common element on a condominium building
Selection of the Low-E coating is one of the most impactful ways to optimize your window design to improve comfort and energy savings.
What are Low-E coatings?
Low-E coatings are not the same as glass tinting. Low-E coatings are very thin layers of metal, often silver, applied to the glass. Tinting can significantly decrease the visible light and colouring whereas Low-E coatings have less of an effect on visible light and more of an effect on the heat transfer and performance in the following 3 ways:
- Reduces solar radiation and heat gain from exterior to interior (SHGC)
- Improves thermal performance of the sealed glazing units (R-Value)
- Reduces heat loss from interior to the exterior (Effective R-Value)
The impact depends on the location and quantity of the Low-E layers applied to the glass. More layers will lower solar heat gain, but product cost will increase. However, reducing solar heat gain may not be desirable, particularly in colder climates and where there is less window area.
How do Low-E coatings affect the appearance and amount of visible light?
The more layers applied to the glass the lower the visible light transmittance (VLT). Clear glass typically allows 90% of visible light through. Each layer of Low E coating reduces visible light by roughly 10%, and will typically add a slight greenish-blue hue.
Let’s take a look at a few case studies to see the impact of optimizing your window design with different low emissivity coatings.
Case Study with 1 Low-E Coating
- 80 unit, 8-storey residential building
- Existing windows: significant air leakage, uncomfortable, and nearing end of serviceable life.
- Window-to-wall ratio: Low (20%).
Owners questioned the available energy savings through window replacement to determine if the savings were enough to justify spending the money now versus in 2-3 years. We assessed standard glass units and confirmed energy savings of about $12,000 / year. We also analysed more expensive double and triple Low-E coatings. Despite improved insulation, there was no appreciable additional energy savings. Factoring in the local climate, window-to-wall ratio, type of heating and cooling systems, client objectives (cost savings vs comfort) and other building characteristics, allowing more solar heat gain through the windows governed and 1 Low-E coating was optimal.
The building’s energy use was modelled and calibrated using the last three years of natural gas and electricity bills to provide confidence in the model and effects of alternative glazing replacements.
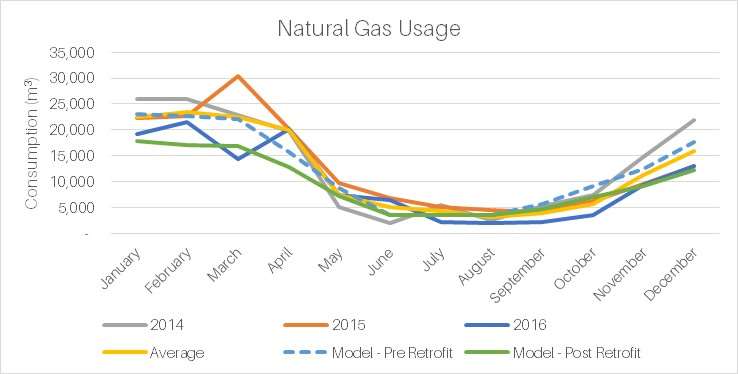
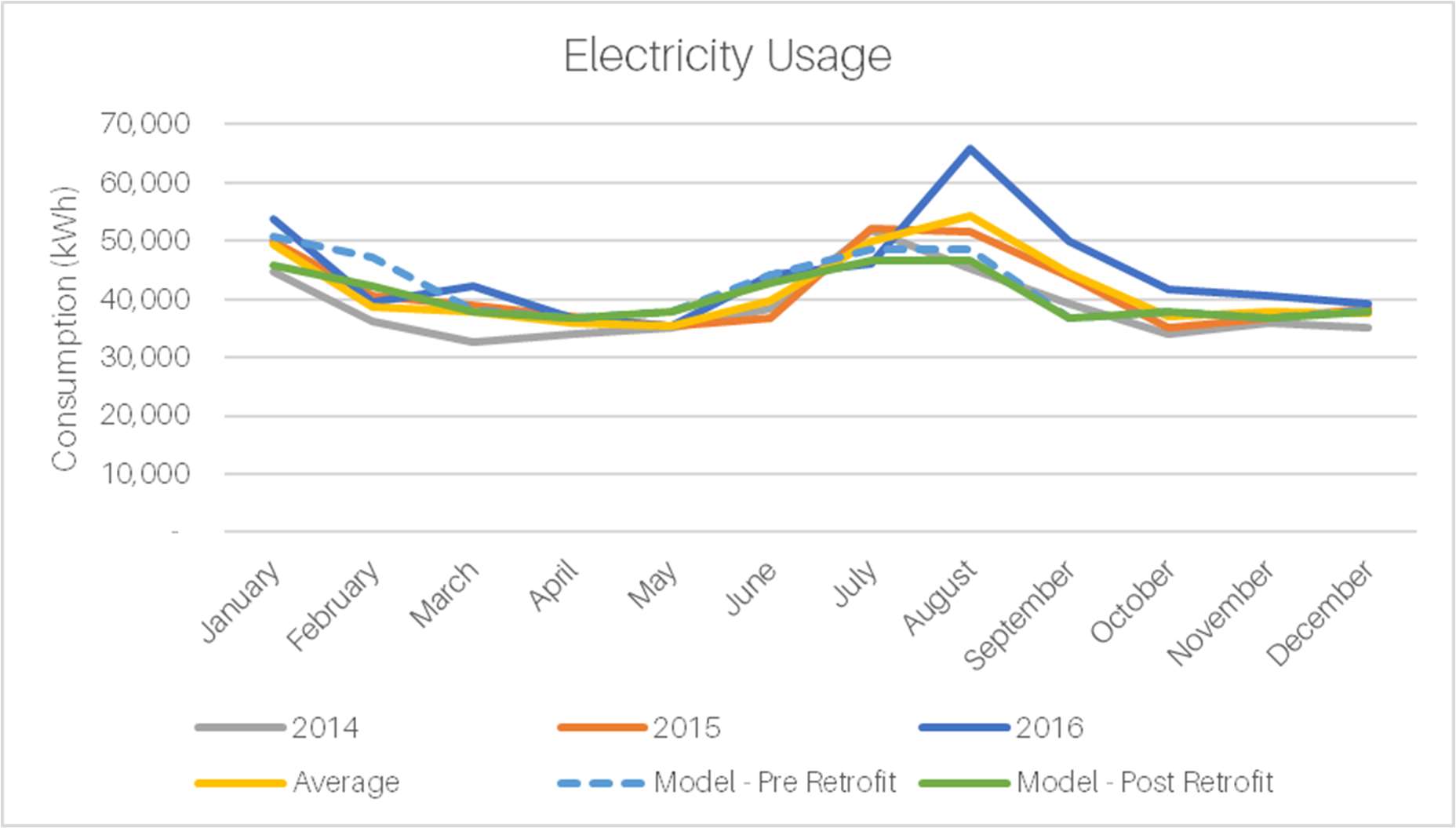
Case Study with 2 Low-E Coatings
- 190 unit, 13-storey residential building
- Existing windows: uncomfortable, high energy use, and at the end of their serviceable life.
- Window-to-wall ratio: Moderate (35%).
- New windows: Double glazed, argon filled sliders with two layers of low emissivity coating.
We evaluated the energy savings from the new windows by comparing the weather normalized utility costs for the 3 years pre-retrofit and the 1st year post-retrofit.
We created a building energy use model and calculated the energy usage pre- and post- retrofit. The results were within approximately 1%. The annual natural gas savings were estimated at
$86,000 based on $0.30 per m3.
We were then able to evaluate the building energy usage for different window retrofits such as single layer low emissivity coatings and triple layer low emissivity coatings.
In this case we found that more solar heat gain with the single layer of low emissivity coating would have cost another $1,300 per year in energy use. We also found that spending the typically 5% more to upgrade to the triple layer would have not provided any further energy savings.
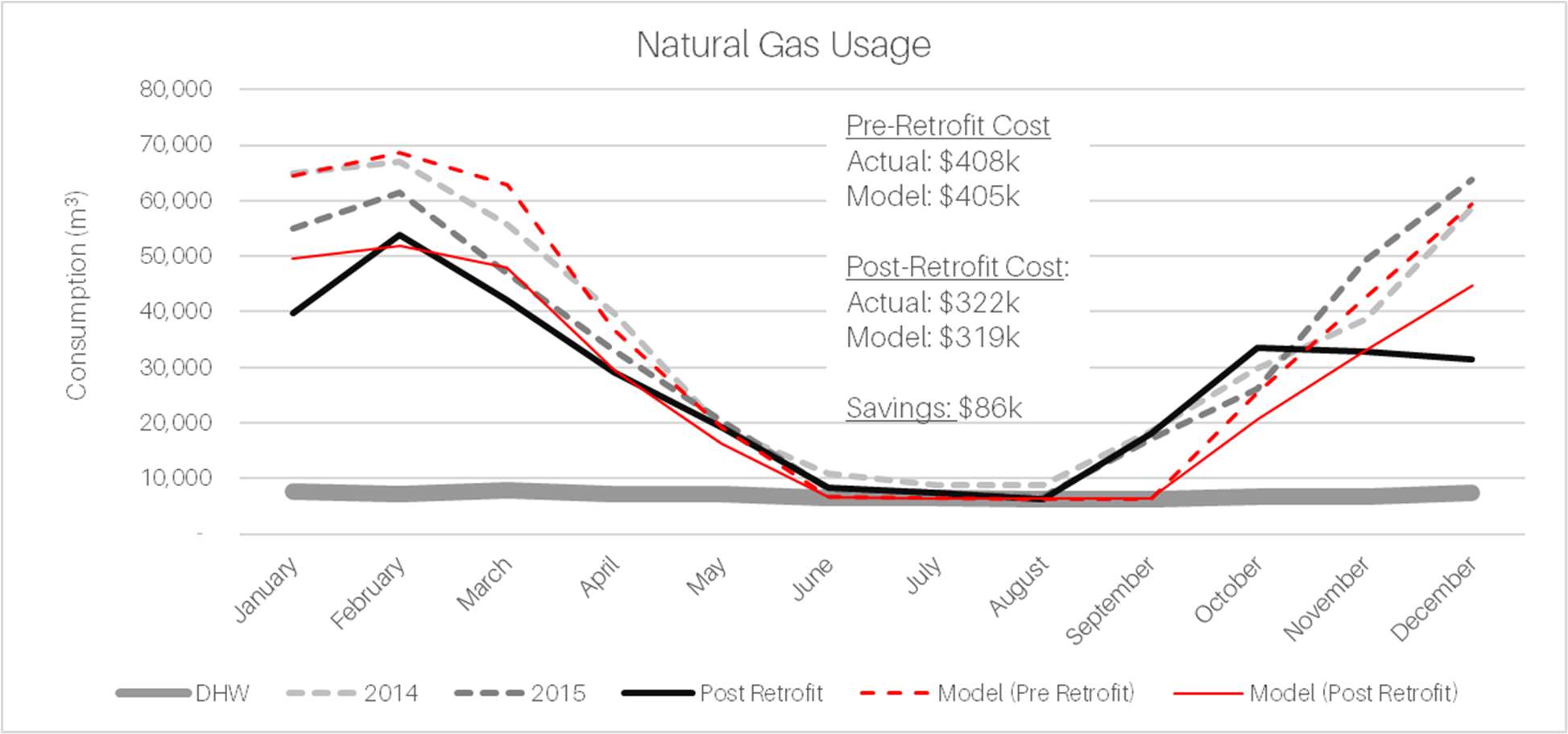
Case Study with 3 Low-E Coatings
- 169 unit, 19-storey residential building
- Existing windows:
- Aluminum framed window wall with uncoated glazing and slider operation
- Window-to-wall ratio: Low (less than 20%)
- Dark - minimal natural light (12% light penetration)
- Minimal air conditioning capacity
- Owner’s objectives:
- Improve view of the lake
- Improve natural light
- Do not increase air conditioning or heating loads
We evaluated the existing windows and calculated the effects of window retrofit options including 2- and 3-layer low emissivity coatings. We created a 3D model of the building using Sketchup to provide visual renderings of the light penetration, view, and overall aesthetic. We calculated the ventilation opening areas, winter-time and summer-time surface temperatures, VLT, solar heat gain, and insulation value (R-Value) so the owners could make an informed decision. In this case, a triple layer low emissivity coating allowed the retrofit to:
- Improve the view - doubling the vision area
- Decrease the air conditioning and heating loads – reducing the solar heat gain and improved thermal performance and air tightness despite the increased glass area
- Improve the natural light – 50% increase in overall natural light and deeper light penetration
despite the 3 layers of coatings.
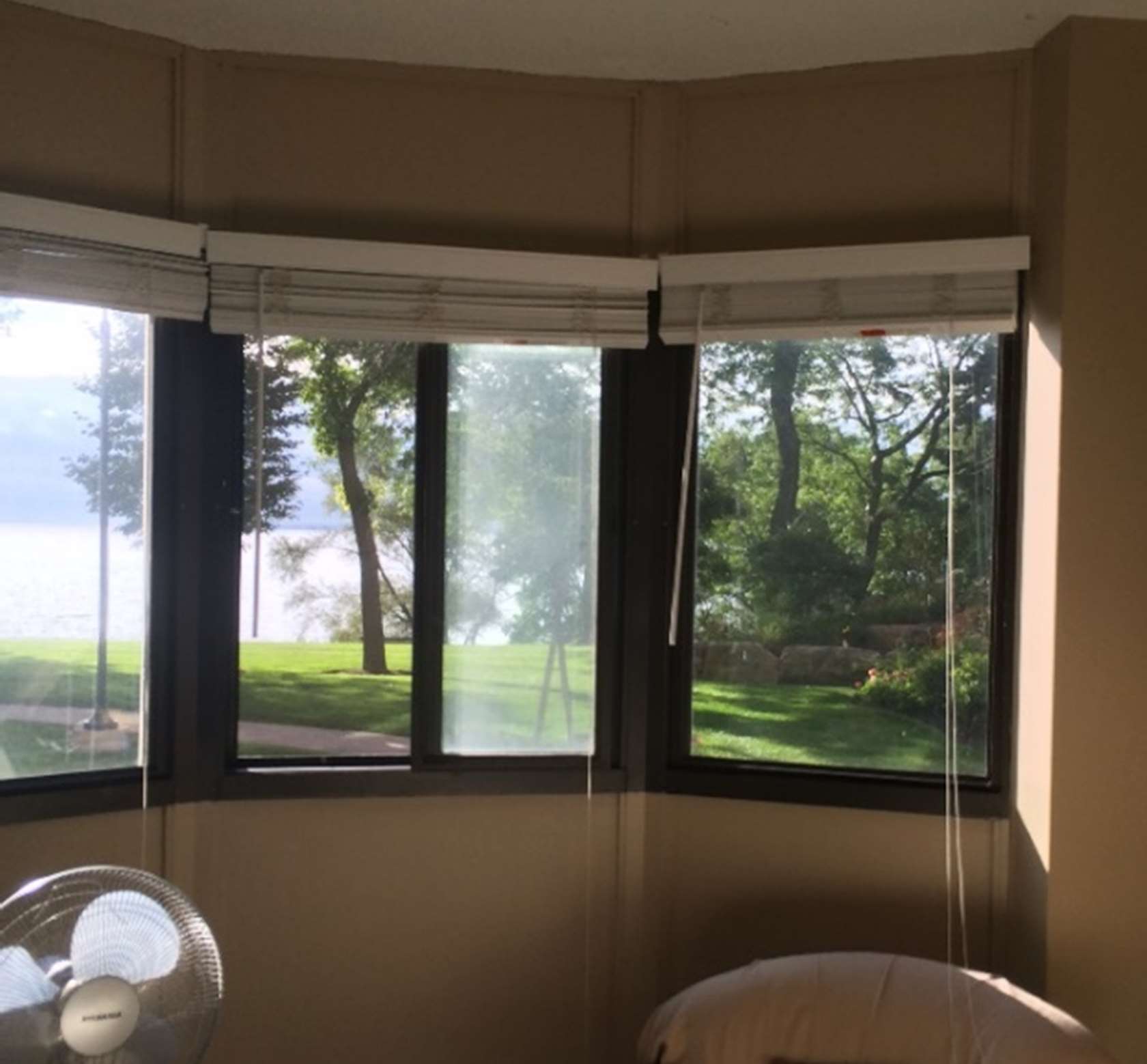
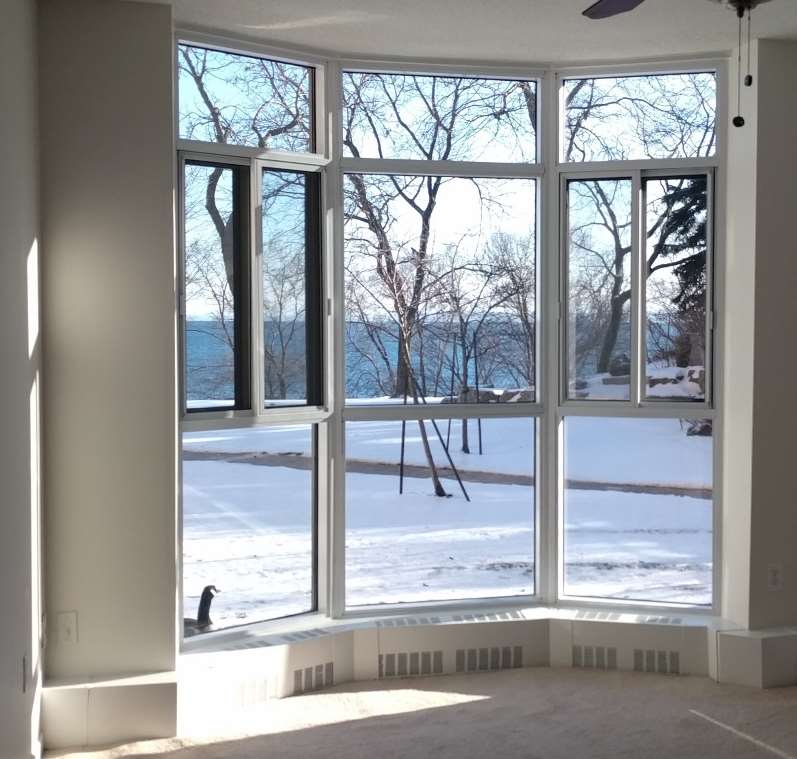
Windows are a significant asset of your community and they directly impact resident comfort and resale values. If you are considering window replacement at your building, we recommend maximizing performance by comparing options to find the optimal design to meet your objectives. In our experience, the estimated utility savings combined with low interest rate environment can justify replacing your windows sooner.
Let us know if you are considering a window replacement project – we’d love to help!